Sizzling Solutions: Reviewing OSHA’s Proposed Heat Safety Standard
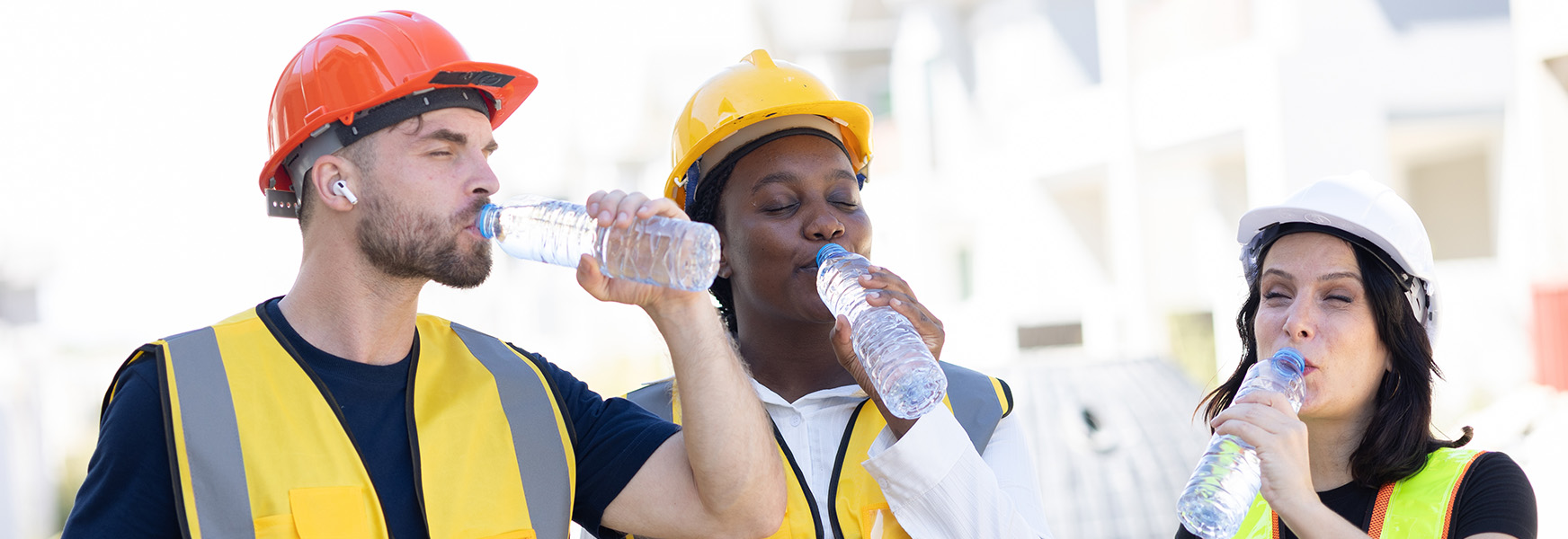
It is hot out there! Working in high heat conditions poses a significant risk. According to the U.S. Bureau of Labor Statistics, each year over 3,000 workers suffer from heat exposure, leading to missed workdays, and there are approximately 40 reported fatalities. Undoubtedly, many more workers experience minor heat-related effects that go unreported.
To address this issue, OSHA introduced a National Emphasis Program (NEP) in April 2022, specifically targeting indoor and outdoor heat hazards. Initially set to expire in 2025, this program can be extended and is already incorporated into the new NEP for Warehouse and Distribution Center Operations. Violations would currently fall under the General Duty clause.
In response to heat hazards, OSHA has been developing a new written standard since 2021. A draft version of the Heat Injury and Illness Prevention Standard has been published and is open for public comment.
Predictably, the proposed standard would require employers to identify heat hazards, devise a plan, and implement controls. Some of the requirements under this proposal for employers with high heat working environments include:
- Calculate and track the heat index, with indoor worksites maintaining a minimum of 6 months' worth of documented monitoring data.
- Develop a heat illness and injury prevention plan (HIIPP) in collaboration with non-managerial employees.
- Review the HIIPP annually and whenever a heat-related injury or illness occurs that meets the requirements for recording on the 300 OSHA log.
- Designate one or more workplace heat safety coordinators to oversee the implementation and monitoring of the HIIPP.
- Offer initial and annual training to all employees, which may include accessing the HIIPP, understanding their rights and duties, contacting the safety coordinator, identifying heat risks, and responding to heat-related incidents.
- Implement the HIIPP at two identified heat triggers: an initial trigger at 80° F heat index (or a wet bulb globe temperature (WBGT) equal to NIOSH Recommended Alert Limit (REL)), and a second high heat trigger at 90° F heat index (or a WBGT equal to NIOSH REL).
- Clearly indicate excessively high heat areas (over 120 degrees Fahrenheit) with warning signs, permitting only authorized trained personnel to enter.
- Provide an ample supply of "suitably cool" drinking water (1 quart per employee per hour) at no cost to the employee, regardless of whether the worker chooses to consume it.
- Establish paid break areas in shaded or air-conditioned spaces and provide "as needed" breaks when the initial heat trigger is reached, along with mandatory breaks of 15 minutes every 2 hours when the high heat trigger is reached.
- Utilize engineering controls to reduce indoor heat.
- Facilitate the acclimatization of new and returning employees by limiting their exposure to work heat on the first day to 20% and gradually increasing it by 20% on days 2-4, without any cost to the employee.
The table below summarizes the proposed requirements:
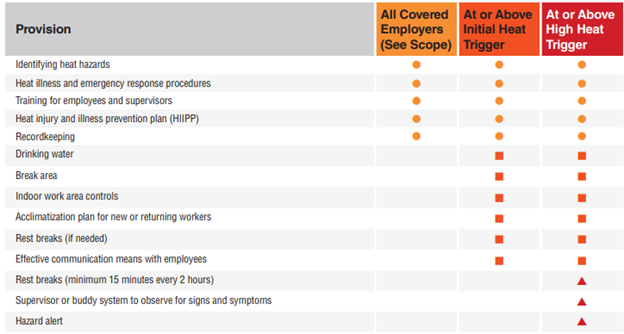
While these requirements have not been finalized and changes are likely, employers can begin to implement some of these best practices now to protect employees from the dangers of hot environments and demonstrate a commitment to prioritizing the health and safety of workers.
Additional resources:
- OSHA Heat Exposure Standards
- OSHA Proposed Rule: Heat Injury Prevention Fact Sheet
- OSHA Heat Illness and Injury Prevention Campaign
MEMIC Blogs:
- The Heat is (Still) On, Especially in These Jobs
- If You Can't Stand the Heat - Go Somewhere and Cool Off!
- OSHA Emphasis on Addressing Heat Hazards is Pretty Cool
- Safer Warehousing: OSHA's National Emphasis Program and How You Can Prepare
By logging into the Safety Director, MEMIC Policyholders can access the webinar, “Can You Beat the Heat?”