The Pressure Is on to Address Hydraulic Injection Injuries
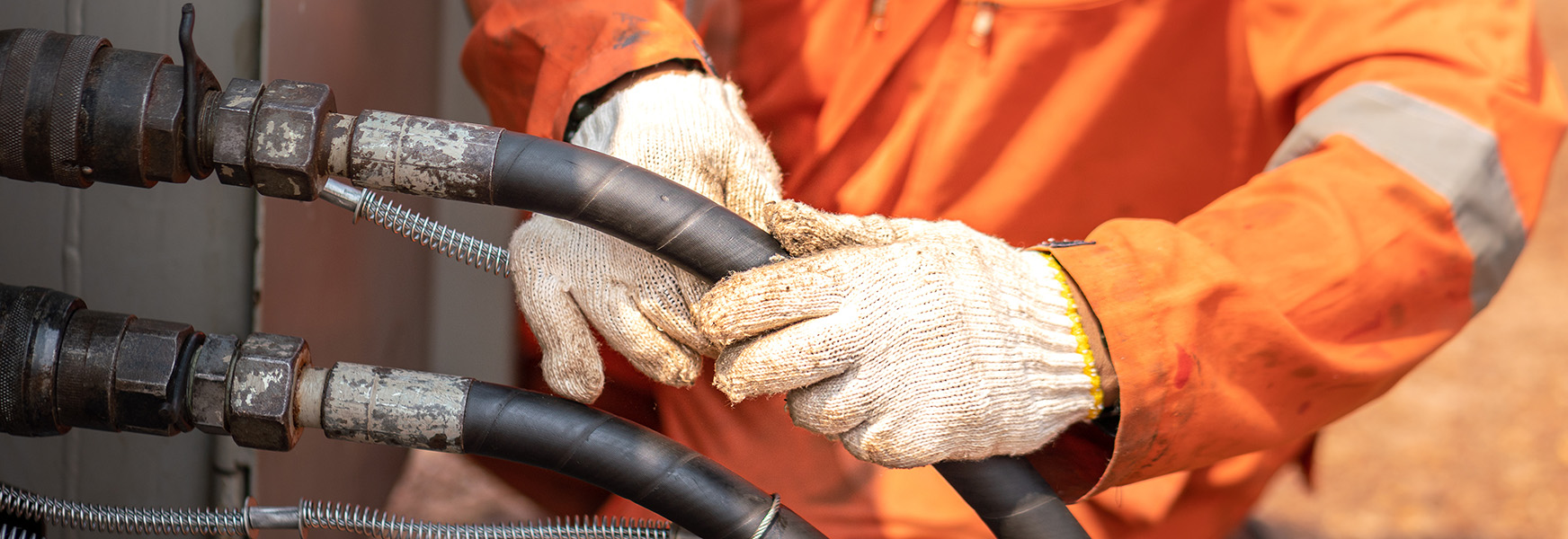
Scenario:
On a typical workday, an employee is tasked with using a boom lift to install windows in a new building at the jobsite. Before operating the lift, the worker conducts a pre-use inspection, which includes visually examining the hydraulic lines for signs of wear or damage. While inspecting the lift, the employee runs their hand over one of the lines and feels a sharp sting through their work glove. Although the pain lasts only momentarily, they dismiss it and continue with the inspection.
Later that evening, the pain intensifies, prompting the employee to seek medical attention. The doctor assumes the employee was injured by a rusty wire or similar object at the jobsite and prescribes pain medication and precautionary antibiotics. However, after several days, the pain worsens, rendering medications ineffective. At the emergency room, the surgeon attempts to save the worker's injured hand but ultimately must amputate the finger.
Unfortunately, it's too late for the worker to realize they have experienced a hydraulic injection injury.
What Is a Hydraulic Injection Injury?
A hydraulic injection injury, also known as a high-pressure injection injury, occurs when a fluid under high pressure penetrates the top layer of skin. Most high-pressure systems operate between 200 and 12,000 psi, but it takes as little as 100 psi to penetrate the skin.
Once the fluid is injected into the skin, it can cut off blood supply, leading to permanent muscle and nerve damage. Prolonged treatment delays can result in the spread of damage from the fingers to the hands, wrist, and eventually the forearm, potentially resulting in limb loss.
Certain pressurized fluids may be more toxic than others, increasing the risk of severe injury or even death. A study published by the National Institutes of Health found an 80% likelihood of amputation when the fluid was paint thinner. This finding is corroborated by a study published in the Journal of Orthopaedic Trauma, which noted that “the risk of amputation after high-pressure injection injury to the upper extremity is highest with organic solvent injection into the fingers.” However, other common hazards include paints, grease, fuel oil, water, air, and cement.
Who Is at Risk?
Individuals working with, inspecting, repairing, or operating around high-pressure systems are at risk of injury. Although these injuries are uncommon, they are extremely dangerous and require urgent treatment, ideally within six hours.
High-pressure equipment is commonly used in industries such as construction, farming, agriculture, industrial, automotive, manufacturing, and engineering.
Preventing Hydraulic Injection Injuries
To prevent these injuries in the workplace, it is crucial to:
- Ensure workers are trained in the proper use and maintenance of high-powered equipment.
- Educate workers about the hazards associated with working around high-pressure equipment.
- Establish routine maintenance and inspection of all equipment to identify wear, damage, and poor fitting connections.
- Implement a procedure for tagging out damaged equipment to prevent further use.
- Store equipment indoors whenever possible, especially in harsh, cold environments.
- Adhere to manufacturer's instructions and recommendations for equipment use.
- Replace hydraulic hose assemblies as required by the manufacturer.
- Never remove protective guards from equipment.
- Avoid using fingers, hands, or cloth-like materials to clean or inspect equipment; use paper or wood instead.
- Encourage workers to report all injuries, regardless of severity.
- Establish an injury management program that facilitates prompt communication with medical providers and includes workplace risk assessment, substance identification, and safety data sheet information.
Implementing these preventive measures and planning for rapid response are essential for reducing the risk of life-altering injuries from high-pressure systems in the workplace. MEMIC policyholders can contact their safety management consultant for further assistance.