No Shortcuts to Safety When Doing It Yourself
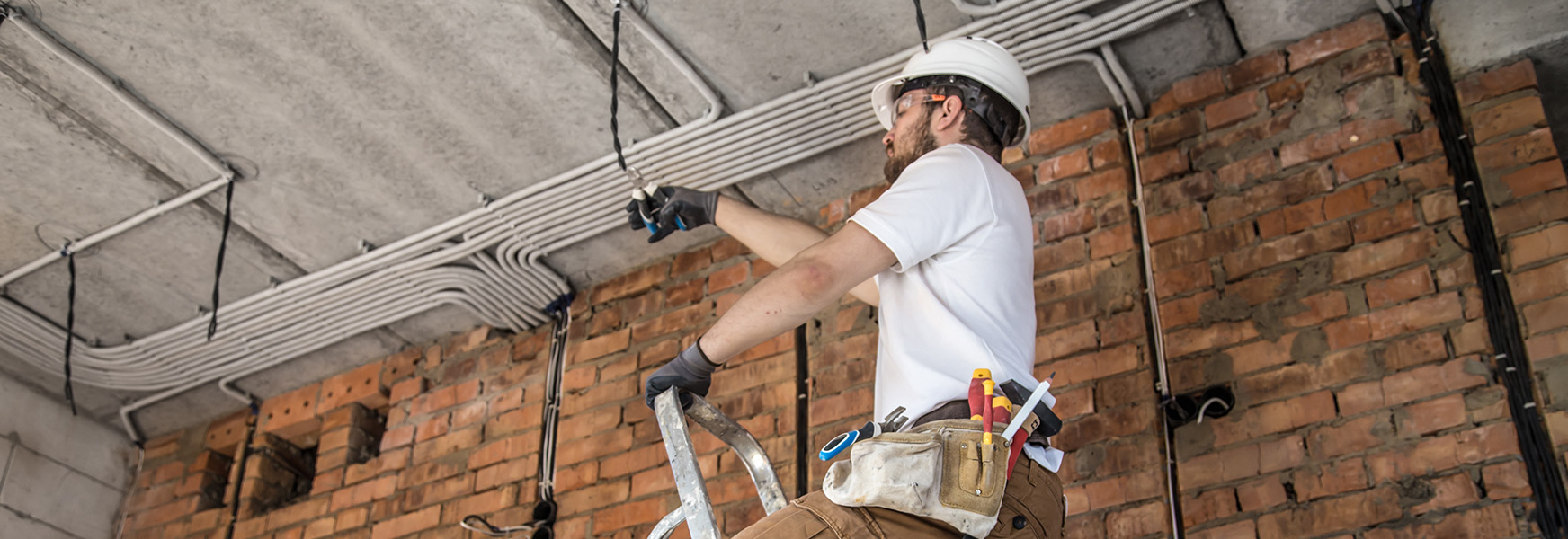
June has now come and gone, and you would really like to get that planned facility upgrade done before cold weather sets in again. You had mentioned it to your go-to contractor last winter, but in checking with them, they did not realize how serious you were, and failed to put it into their calendar. They are now busy and shorthanded and will likely be a year and a half before they can get to you.
With contractors of all professions facing staff shortages and backlogs, there is motivation for facility managers and homeowners alike to consider self-performing repairs and upgrades. These could range from leveling the parking lot to re-facing a building to installing an outdoor power supply.
Regardless of the scope of work, it’s likely you will need some additional tools and equipment. If cost of ownership is a concern, renting is a great option. Your local rental house will likely have a modern inventory that is up to date on service and repairs. They are also required by ANSI to provide a basic level of training for all equipment they rent. Keep in mind however, that an extra tier of training will still be needed once on site to account for site-specific operational hazards.
It’s tempting to jump right in and tackle the project once the necessary materials, tools, and equipment have been acquired. But before starting, review the following checklist to help avert unforeseen circumstances:
- Are permits required?
- What OSHA regulations may apply to those performing the work?
- Are workers adequately trained?
- Are employees working near rented equipment familiar with its operating space and/or blind spots?
- Are there standard operating procedures that must be adhered to?
- Have all hazards in the work area been accounted for and managed?
The following are key activities and their significant associated risks that should be evaluated before starting work:
Trenching and Excavating – If facility upgrades require work below ground, refer to OSHA's resource page to ensure all workers are protected from related hazards. Look at the trenching and excavation - construction page for more details on OSHA standards. Be sure to contact your state utility service to locate and mark any underground utilities to ensure the excavation can be done safely. In New England, this service is provided by DigSafe, which typically requires a 72-hour notice. Be sure to check your state specific requirements.
Concrete/Masonry – The potential for overexposure to respirable crystalline silica is of significant concern with this type of work. OSHA's online guide supplies information to recognize and control this hazard.
Work at Heights - Falls from elevation continue to be a leading cause of workplace injury and fatality. Consider OSHA's fall protection guide to ensure workers are adequately trained when performing work where fall hazards exist.
Non-routine tasks often have hazards and/or risk factors that can lead to worker injury. Take a close look at work that is new or unusual and make an honest evaluation as to whether your team can complete the work safely.
After careful consideration, if you still have uncertainties about a proposed project and you’re insured with MEMIC, contact your safety management consultant for assistance.
Check out these other MEMIC blogs: