Preventing Traumatic Brain Injury: Protective Measures from Head to Toe
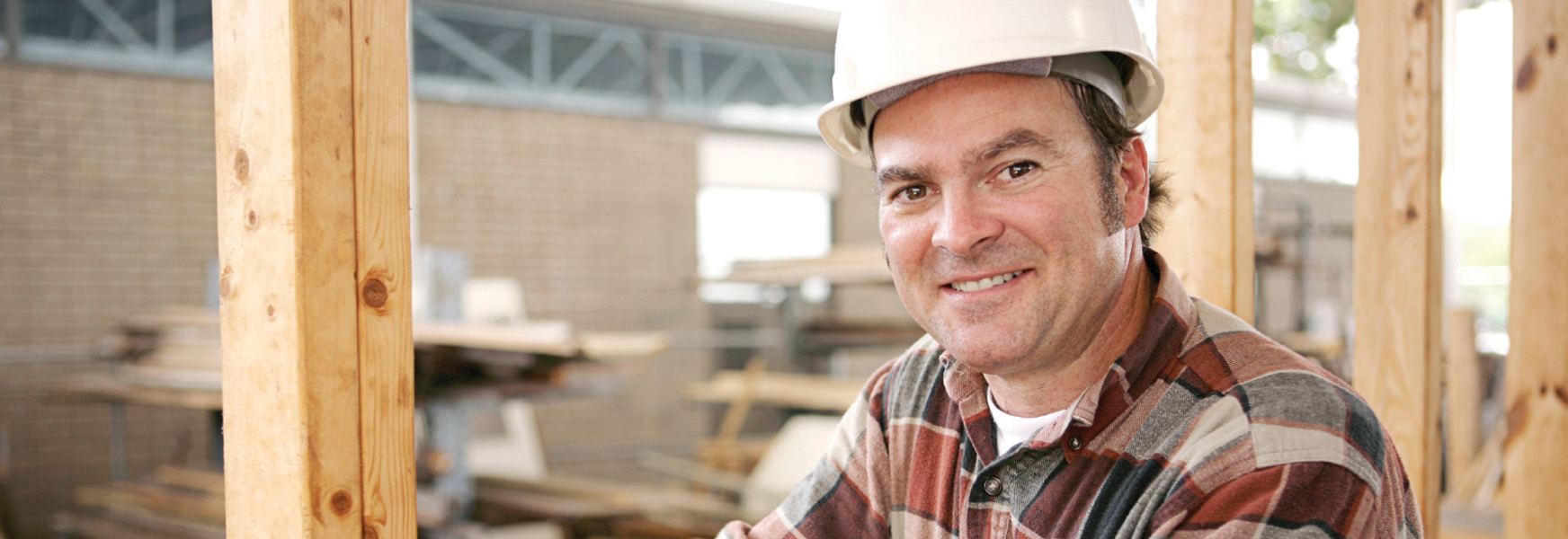
You’ve been warned. You’ve seen the statistics, traumatic brain injuries (TBI) contribute to approximately 30% of all injury deaths.
So we all just need to wear a hard hat whenever there is the slightest chance of risk, which is all the time. Problem solved, you can forget that March is Brain Injury Awareness Month.
But we live and work in the real world. People don’t wear a hard hat all the time, protecting your head takes more than that. It takes using your head and being aware of your surroundings. So while the more obvious means of preventing traumatic brain injury is through head protection in the form of helmets and other protective headgear, let’s explore each of the three leading causes of TBI with regard to preventative measures employers and employees need to take. When considering TBI-related emergency department visits, hospitalizations, and deaths in the United States, you might think being struck by or against an object would be the leading cause, but it’s only 15% of TBI. The leading cause, at a whopping 47%, is falls. Motor vehicle crashes come in at third with 14%.
Falls, as the leading cause of TBI, also represent the leading cause of private sector worker deaths in the construction industry (excluding highway collisions). OSHA defines a fall hazard as “any condition on a walking-working surface that exposes an employee to a risk of harm from a fall on the same level or to a lower level.” The threshold height levels for fall protection are only 4 feet for employees in general industry, 6 feet above a lower level for the construction industry, and 10 feet for work on scaffolds.
While fall protection is not required for portable ladder use, OSHA recently updated its walking-working surfaces and fall protection standards with timeline requirements for fixed ladders over 24 feet to be equipped with a personal fall arrest system or ladder safety system. The standards include provisions for ensuring employees are trained on fall hazards and equipment covered by the rule. Training needs to be conducted by a qualified person with the topics including the nature of fall hazards and how to recognize them, the procedures to be followed to minimize the hazards, and the correct procedures for installing, inspecting, operating, maintaining, and disassembling the personal fall arrest systems the employee uses. The training requirements also include proper hook-up, anchoring, and tie-off techniques for personal fall arrest systems.
With regard to falls on the same level, proper housekeeping is essential to limit clutter from tools, equipment, debris, and other materials accumulating in the work area that could result in a slip, trip, and fall head injury. Employers and employees should adhere to the maxim of a place for everything and everything in its place. You’ve got to think S.A.F.E. – Surface, Awareness, Footwear, Environment (which was covered in our recent slip and fall prevention series by Peter Koch).
With the second leading cause of TBI being struck by or against an object, a blow to the head from objects falling off an elevated work platform or striking a low-lying overhead structural member comes to mind. OSHA’s general requirements for head protection in 29 CFR 1910.135 state the following:
- The employer shall ensure that each affected employee wears a protective helmet when working in areas where there is a potential for injury to the head from falling objects.
- The employer shall ensure that a protective helmet designed to reduce electrical shock hazard is worn by each such affected employee when near exposed electrical conductors which could contact the head.
The American National Standards Institute (ANSI) establishes the criteria for industrial head protection in its Z89.1 set of standards. The consensus standards categorize hard hats by impact type as well as classification by voltage protection. A Type I hard hat offers protection by reducing the force of impact on top of the head and a Type II hard hat has the additional feature of lateral impact protection. The three hard hat classifications for voltage protection are Class G for general purpose with limited protection (up to 2,200 volts), Class E (electrical) providing protection up to 20,000 volts, and Class C (conductive) offering no protection from electrical conductors.
As with any type of personal protective equipment, hard hat components including the shell, suspension system, and chin strap (if applicable) need to be regularly inspected, maintained, cleaned, and properly stored. In order to thoroughly inspect the hard hat shell, the application of decals should be limited with painting of the shell avoided where some paints and thinners may compromise protection effectiveness. Only hard hats marked with a “reverse donning arrow” symbol can be worn frontwards and backwards in accordance with the manufacturer’s wearing instructions. While OSHA does not specify an end of service life for hard hats, most hard hat manufacturers recommend replacing hard hats every 5 years under normal use conditions and at two year intervals when working in harsh environmental conditions.
Another type of head protection device is a bump cap that offers protection from minor bumps and scrapes when working in areas with low head clearance. However, bump caps are not ANSI-approved and do not provide protection from falling or flying objects. In a letter of interpretation related to the wearing of bump caps for manhole entry and service/maintenance work within, OSHA states bump caps “would not provide adequate employee head protection for all exposures in manholes because they are not constructed in a manner to provide the protection required.”
Turning to the third leading cause of traumatic brain injury, the CDC reports more than 37,000 people are killed and 2 million are injured each year from motor vehicle crashes in the United States. Additionally, the US crash death rate in 2013 was more than twice the average of other high-income countries. With an increase in roadway construction and repair (to an aging highway infrastructure), motorists and workers in road construction work zones bear a greater risk of vehicle-related injury. Here are 10 safe driving tips for motorists/employees involved in business travel.
- Obey speed limits
- Always wear a seatbelt
- Don’t text or talk on a cell phone while driving
- Don’t drive under the influence of alcohol or controlled substances
- Always use turn signals
- Use headlights in inclement weather
- Inspect the vehicle regularly (tire tread, fluid levels, etc.) and keep it well maintained
- Leave early and plan to arrive 10-15 minutes sooner than expected
- Drive defensively, keep your eyes moving and check surroundings in your mirrors every 6-8 seconds
- Pay attention to all road signs, particularly when approaching road construction zones (click here for more safe driving tips)
OSHA standards that regulate work in traffic are found in 29 CFR Subpart G with Part VI of the Manual on Uniform Traffic Control Devices (MUTCD) incorporated by reference. The MUTCD requires employers to assign a competent person to each job-site. The definition of a competent person is “one who is capable of identifying existing and predicable hazards in the surroundings, or working conditions which are unsanitary, hazardous, or dangerous to employees, and who has authorization to take prompt corrective measures to eliminate them.” The competent person has the responsibility to conduct frequent job-site inspections including materials, equipment, and traffic control devices along with conducting regular, ongoing worker safety training.
The key to worker safety is visibility through the wearing of high visibility safety apparel meeting the requirements of ANSI 107 to ensure the worker can be seen from all sides. Temporary traffic control zones need to be designed with 1) an advance warning area, 2) transition area, 3) activity area, and 4) a termination area. Motorists need to be alert to signs, signals, and barricades by keeping their eyes on the road and their hands upon the wheel.
When thinking of head protection, the three leading causes of traumatic brain injury reveal a need to consider more than just the use of protective headgear. While a hard hat is most evident, a full-body harness with lanyard, high visibility clothing, and proper footwear with or without toe guards are essential under specific work conditions. Remember, PPE can help protect your head from hazards, but your first line of defense is using your head to eliminate hazards and implement engineering and administrative controls.