How to Deliver Safety to the Loading Dock Environment
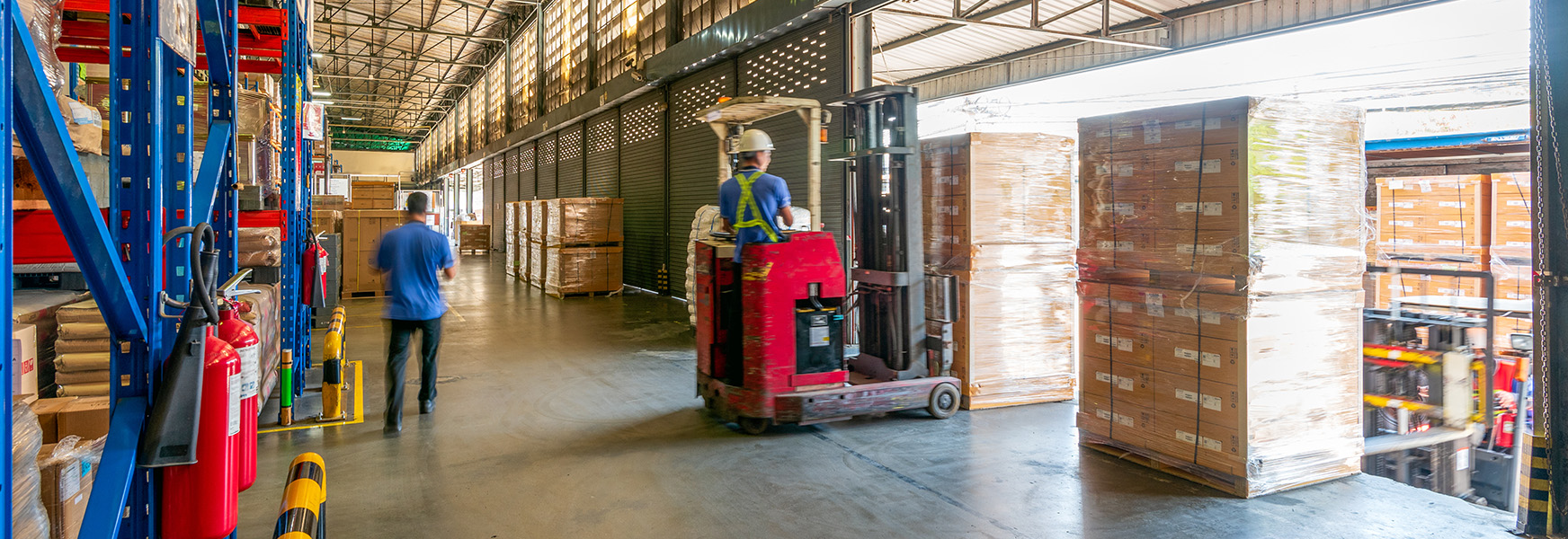
While loading docks typically provide sufficient space to handle freight safely, they can sometimes be a hazardous place for workers. As material is moved for shipping and receiving, limited time and productivity demands can lead to accidents. Loading dock personnel and those not directly involved in these operations must be alert for hazards.
OSHA’s most recent data estimates 35,000 to 62,000 injuries occur annually from forklifts. In 2021, OSHA investigated 15 loading dock accidents with 12 resulting in fatalities. Slips, trips, and falls, including falls from the dock edge, are the most frequent injuries reported around loading docks. Being crushed between trucks and docks is the leading cause of worker fatalities.
Root causes of incidents include lack of training, poorly defined procedures, and human error. Other common hazards and controls are as follows:
Loading dock hazards:
- Slips, trips, and falls caused by poor dock conditions, including lack of housekeeping, uneven or broken flooring, open dock edges, and insufficient lighting
- Uncontrolled movement of mobile equipment around docks and pedestrians, causing potential for struck-by or crush injuries
- Increased fall risk from unsecured or improperly used dock plates that leave large, unguarded openings
- Unsecured freight that causes struck-by incidents
- Open dock doors and unguarded edges responsible for falls from height or forklift rollover
- Poor condition of trailer floors that people and equipment can fall through
- Lack of safety training specific to loading docks
Loading dock hazard controls:
- Develop formal loading dock safety policies and training and include all personnel who will be in the area.
- Utilize wheel chocks, or barrier vehicle restraint systems, to prevent trailer creep.
- Clearly define the loading dock area and designate safe walking zones with signage and high-visibility paint.
- Use colored lights to signal when it is safe for material handling equipment or personnel to enter loading dock areas.
- Utilize physical barriers along dock edges when not in use to prevent accidental falls. (OSHA requires fall protection on any dock higher than 48 inches.)
- Properly secure loose freight by shrink-wrapping or banding loads.
- Ensure workers are trained in loading dock material handling equipment operation.
- Inspect the trailer floor to ensure it will support the forklift and load.
- Train workers on the proper inspection and use of dock plates or ramps.
- Provide adequate lighting in the loading dock area and in trailers.
- When backing out of trailers, sound the forklift horn and check for workers in the area.
Though this list may seem daunting, remember that your MEMIC safety management consultant is available to help you identify workplace-specific hazards and assist you in prioritizing changes to improve safety and protect your employees.
Other Resources:
-
MEMIC Safety Director: MEMIC Safety Minute, Loading Dock Safety – Forklifts