Do You Have Accident Repeaters or Accident Repetition?
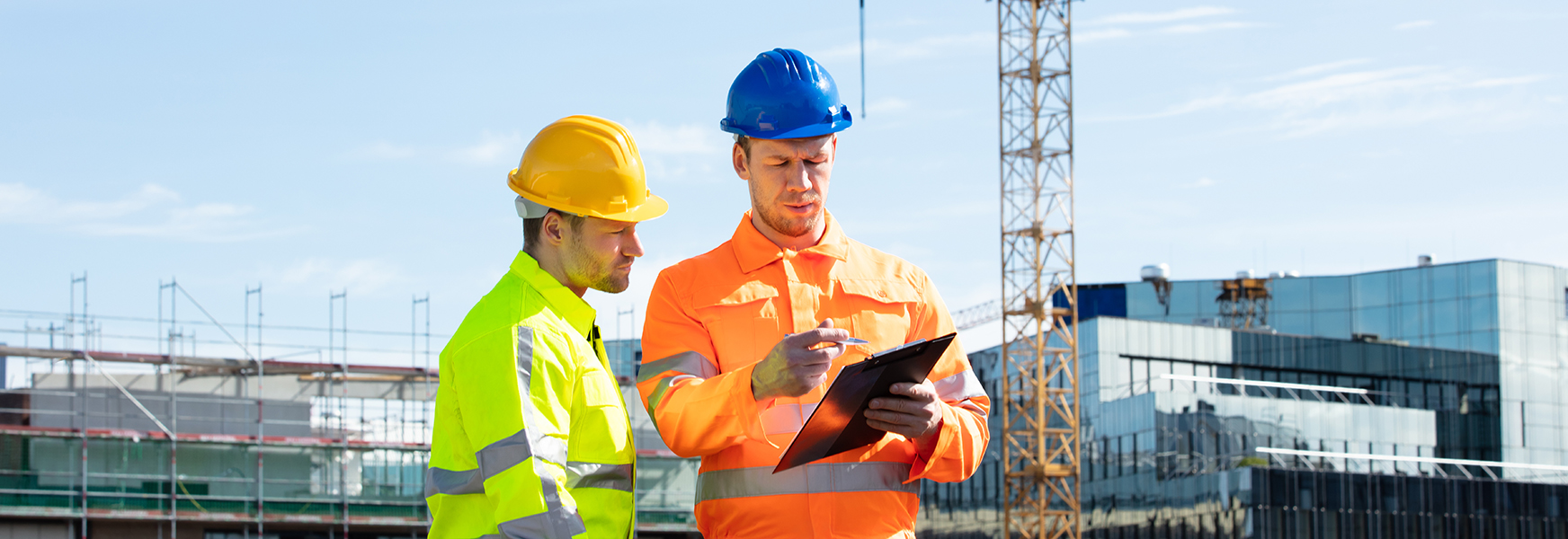
Are the same employees getting hurt again and again? Why does it seem that 20% of employees account for 80% of workplace injuries? Are they careless, or not paying attention? Maybe it’s the job; is it too difficult? Are supervisors doing their jobs? The idea of “accident repeaters” has long been an issue in the world of safety. Accident Repeater programs have even been created to help determine why someone keeps having accidents – as if it’s a choice, or they’re doing it intentionally. Since intentional injury is rare, the root causes will likely be found elsewhere.
Accident repeater programs focus primarily on employee behavior. Typically, this means putting a person in front of a group of their superiors and peers who ask questions to determine the cause of the incident and initiate corrective action. This process can easily include the underlying premise of “what did you do wrong this time?” or “are you trying to get out of work?” or “this wouldn’t have happened if you followed the rules.”
The more contemporary view of this issue is to look at these incidents as “accident repetition.” This change in wording recognizes the occurrence frequency but does not assume or imply where the cause lies.
Accident repetition recognizes that the same person is injured on the job with some frequency, but the process to determine cause and corrective action remains the same as all properly completed accident investigations. This process not only looks at the “people” elements, but looks equally at equipment, materials, training processes, and environmental factors in determining the root cause(s).
Accident repeater programs focus on the worker alone. Although unsafe acts are more often the cause of workplace injury than unsafe conditions, the proper investigation will go much further and often identify multiple causal factors. Focusing on behavior alone can open the door to bias and unfair treatment. If investigators have preconceived ideas, it’s likely the end result will be a flawed investigation. Accident repeaters are often thought to be looking to get out of work or they just aren’t tough enough to do the job.
Rather than labeling injured workers as accident repeaters, consider repeat incidents involving the same people to be accident repetition. This approach takes a more wholistic view. If accidents are occurring to the same individual, then finding all of the pertinent root causes is vital to the overall success of any safety program.
Working with employees to improve their personal safety and the safety of those around them should always be the focus. Evaluate their skill level and train them to increase their personal safety and situational awareness. This will help them to better understand the factors that led to the accident. Educate employees to recognize hazards, train them to understand safe operating procedures (SOP), require the use of PPE and other prevention tools, and work to improve safety communication skills. Creating a Personal Improvement Plan with specific actions employees can take to elevate their individual safety actions is a great way to eliminate accident repetition.
Accountability is a significant element in safety programs. If discipline is necessary due to circumstances that resulted in an accident, it must be clear, consistent, equitable, and timely. Follow company policy and ensure upper management offers support at every step.
Focus organizational attention and activity on conducting good accident investigations, whether for accidents being incurred by the same person repeatedly, or for any members of your workforce. To learn more about accident investigation programs, components, and techniques, check out the MEMIC resources available to our policyholders within the Safety Director at memic.com.
Posted by Dave Darnley and Jennifer Campbell