Are Your Employees Safely Oriented?
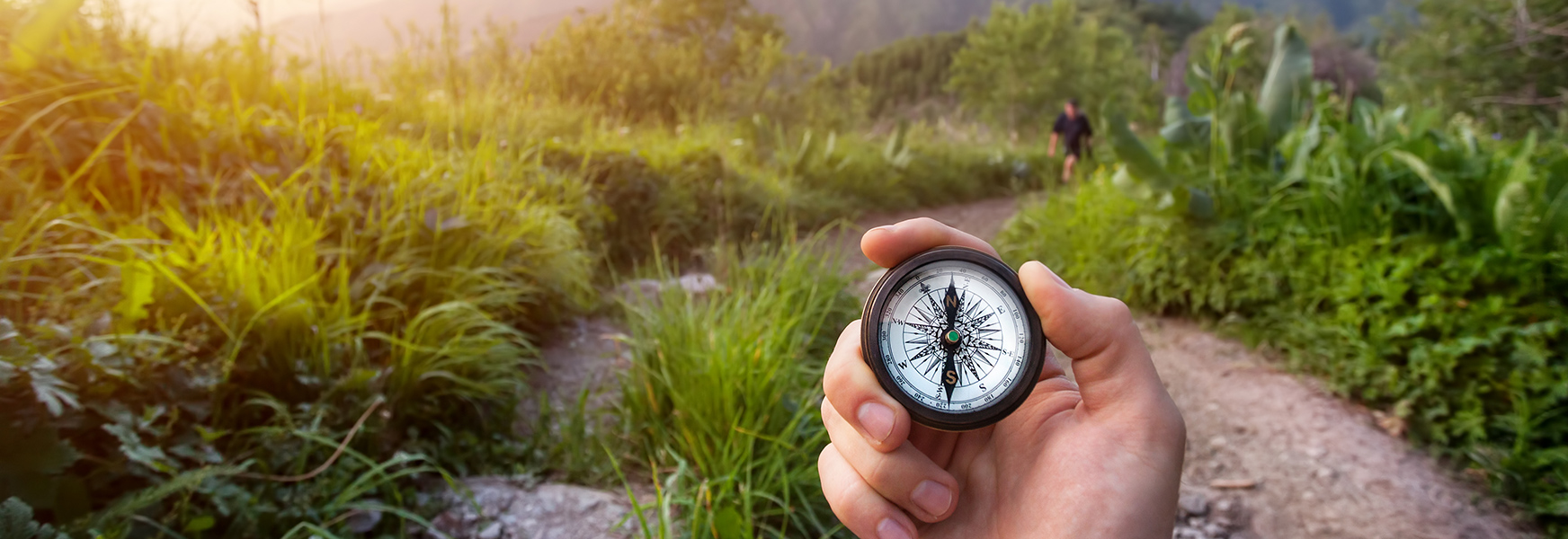
Hiring and retaining good employees is a challenge for most employers, especially given the historically low unemployment rates. The hiring process is time consuming and resource intensive; and this is before we even get the new employee in the door for orientation. Once the interviews are completed and the job offer has been accepted, it’s time to ensure that our new employee gets off to a good start with an effective orientation process.
Considering that we are a safety company, we are going to focus solely on the safety component of the orientation process. We’ve all been new employees at some point and understand that there’s a lot of information covered in a relatively short amount of time. Read this handbook, sign these forms, choose from these benefits, watch these videos, etc… The whole process can be overwhelming and we cannot expect our new employees to retain all of the information presented.
The importance of thorough safety orientation can’t be understated. In 2017, 32% of lost time injuries were suffered by employees with less than a year of tenure according to the Bureau of Labor Standards. Given the high injury rate for new employees it is clear that a comprehensive orientation focused on hazards and controls is critical.
This process must include a “hands-on” component. People will remember only a small fraction of what they hear, a little more of what they see, but far more of what they actually do. This is an opportunity for the new employee to shadow someone with experience and learn about the site-specific hazards that exist within their work area. Leaving new employees to discover workplace hazards on their own simply leads to more injuries. Consider the story of Brad Hurtig who, as a young man, lost both hands in an industrial incident on his first night on the job. Brad has gone on to become an effective motivational speaker, but his life was certainly changed forever. No pun intended, but a thorough hands-on orientation for Brad might have resulted in him keeping his hands. Here are some items to consider:
- Identify a core group of experienced employees to conduct the hands-on/site-specific training for new hires. These trainers should be employees who constantly demonstrate safe work practices.
- Create a checklist for your trainers to use as a guide for new hire training. The checklist should include work areas, specific tasks, and safety related procedures. Identify higher risk operations to be sure employees are aware of the most severe hazards. Heavy equipment operation, material handling, forklift traffic flow, and chemical exposures are prime examples. The trainer and new hire should sign the completed checklist and retain it in a filing system.
- Have the new employee demonstrate a working knowledge of the equipment they will be operating. This should include the safety procedures for equipment failures and/or when material becomes jammed. Lockout/tagout is certainly part of the essential training for both authorized and affected employees.
- Follow-up with the new hire on a regular basis to ensure safe work practices are followed and to provide immediate feedback as needed. Most employers have a 90 day probationary period, but supervisors or managers should be checking in with them much sooner than that.
Remember, new employees may be reluctant to ask questions for many different reasons. This is why it’s so important to ensure that they receive the proper safety training before working on their own and that someone is checking in with them on a regular basis. This can also help with retention as it creates a sense of comfort and belonging for the new employees. It also demonstrates your commitment and expectations as a company when it comes to safety.
For more information on new-hire orientation check out MEMIC’s free resources in the Safety Director. For ongoing safety training requirements for all employees, OSHA has published a document entitled Training Requirements in OSHA Standards. This is a comprehensive outline of all regulatory training required for both the General Industry and Construction industries.