Falls from Rolling Chairs – Yeah, it’s a Thing
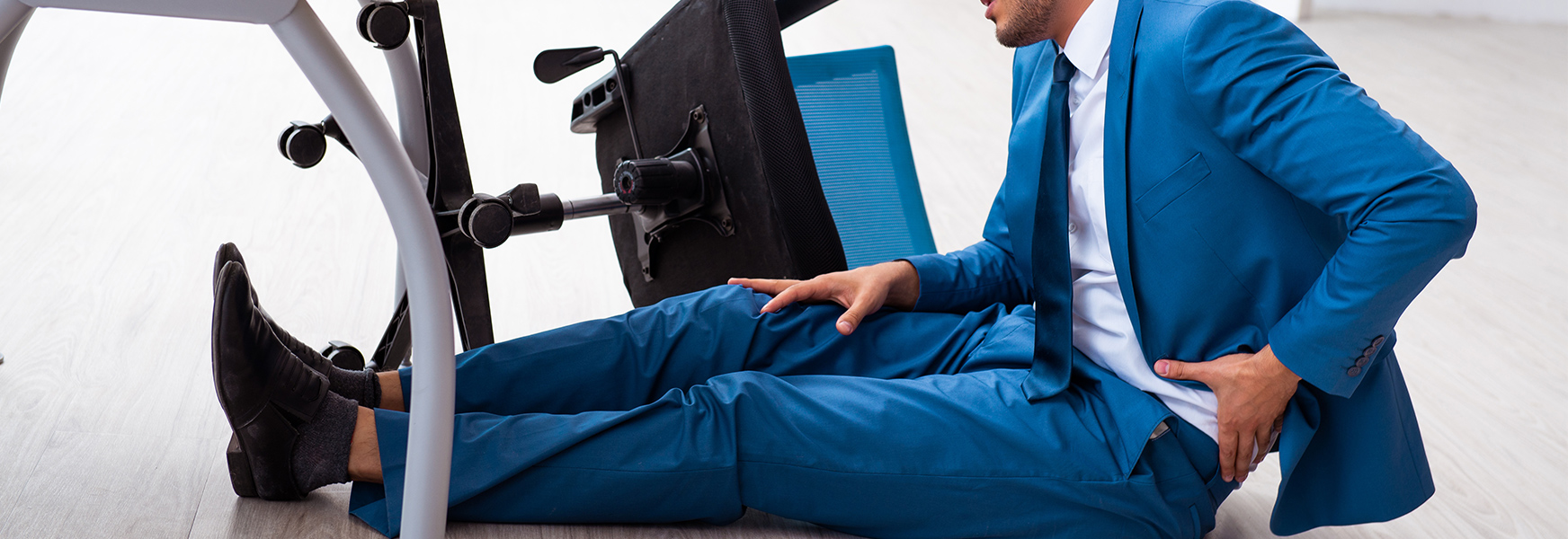
As the weather turns colder, slip and fall incidents begin to rise. A recent Safety Net post, Fall In Down Without Falling Down was a reminder that fall is beautiful but does present a seasonal hazard. Falling is certainly not limited to the outdoors. Have you ever found that the chair you are trying to sit in rolls away from you too easily? Maybe like the chair is gliding on ice? My professional experience is in healthcare where this type of incident seems to be more prevalent. Among MEMIC policyholders 45% of the falls from chairs occurred in healthcare facilities. Recently, while following up on an injury involving a chair-rolling incident, I uncovered some interesting causes that may pique your interest. This post is not meant to be about ergonomic chairs; however, ergonomic chairs are the only chairs providing enough choices in wheels to fit the varied workstations (and flooring) in healthcare facilities. Naturally, many of the issues identified, as well as the solutions offered could apply to employers across many industries. Any office setting that has employees sitting in chairs during the workday could be prime real estate for one of these incidents.
Over the past three years (2017-2020), MEMIC policyholders have sustained over 400 injuries related to falls from chairs. In some instances, the chair “slid out” and in other instances the chair collapsed from under the employee. One chair incident, in which the chair slid out from under the employee, resulted in losses of $159,000. Similarly, a collapsed chair caused an injury to an employee which cost $140,000.
Falls from chairs seem to be swept aside with a cavalier attitude “what can we do anyway?” There are several steps to prevent these types of incidents and potential injuries.
Casters and wheels are terms often used interchangeably; however, they are not the same. Simply stated, a chair wheel is the round object that rolls on the floor. The caster is the entire component- the attaching frame or bracket, any swiveling hardware, and the wheel. The focus here is the wheel material and how it interacts with the flooring.
Wheels are designed to work best on specific flooring types. Healthcare settings generally have hard surface flooring such as tile, vinyl, laminate, or hardwood. Office spaces in other industries are often carpeted, and these floors require a very different wheel.
Wheels are available in many materials but are in two basic categories. Hard wheels are made of nylon or metal. They can glide (instead of roll) on tile, linoleum, or vinyl flooring. This is why the nurse attempting to sit on the rolling chair found that with a little nudge, “the chair just flew out from under me.” Unfortunately, a serious injury resulted. Hard wheels should only be used on carpet.
Soft rubber or polyurethane wheels are best for hardwood, tile, marble, cement, travertine, linoleum, and vinyl. The soft wheel provides the best floor protection for these floors, as it has a slight “give” to conform to the hard floor and are less likely to glide away from someone attempting to sit down.
Office chairs made for the homeowner are less expensive and wheels are usually a hard nylon for better chair rolling on carpet. They may also have only four legs and be more prone to tipping. A chair designed for the workplace should have five legs (see OSHA’s Workstation E-Tool), be fully adjustable, and have the proper wheels for the workstation. Not only is this a safer chair in regard to falls, but it also provides better ergonomics for the user and even promotes better productivity. Researchers have found that employees are 17% more productive when trained in ergonomics and provided an ergonomic setting.
So, this information begs the question – “How do I know the difference between the hard wheels and soft wheels?” Can you press into the wheel with a ballpoint pen and leave a dent? If so, then it is a soft wheel. If you can’t dent it -it’s probably hard – for use only on carpet.
Chairs also have recommended weight limits. In an environment where many workers are using the same chair on different shifts this must be considered. A typical weight rating is 250 pounds, so if there are any potential users that weigh more than that a different chair or caster assembly may be required.
Lastly, chairs do not last forever. The life span is generally less than seven years and can be significantly less with heavy use. Chairs are a good investment for both safety and productivity so proper maintenance is required, and they should be replaced when indicated. A yearly chair evaluation will help to bring any issues to light which may cause injury later. Policyholders have access to the MEMIC Safety Director which has published several chair safety documents including a Chair Evaluation Checklist.
Chairs are often taken for granted even though they are an essential tool in the workplace. Selecting the proper chair including the appropriate casters and wheels can make a significant improvement in employee comfort, safety, and productivity. For more information on caster and wheel types and selections check out this resource from Caster City.